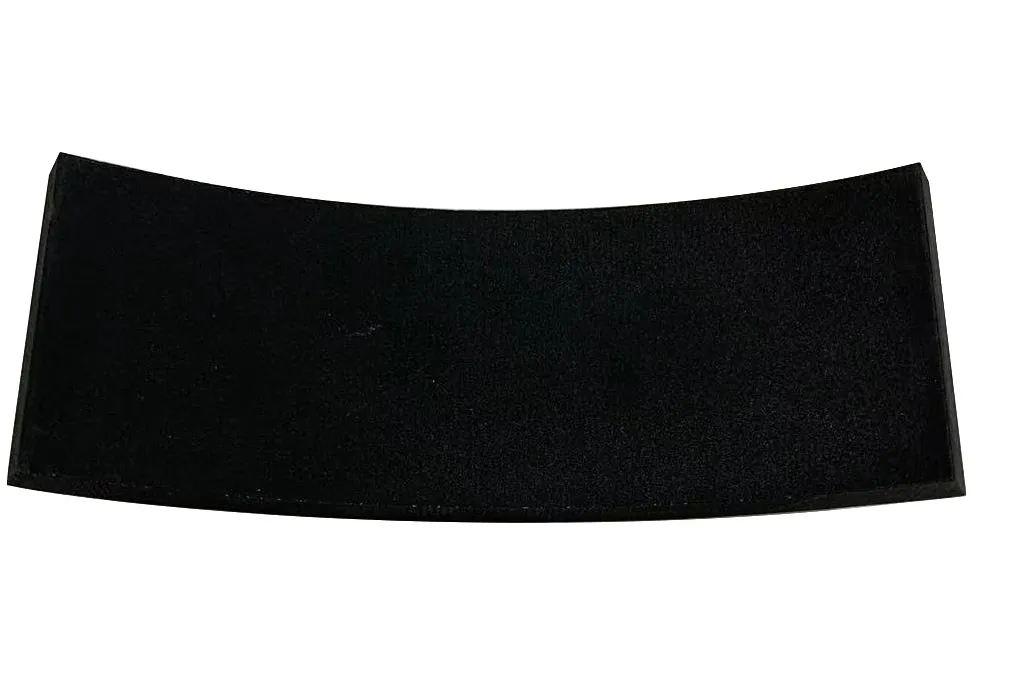
The role of Friction Lining
Friction lining is a critical component used in a wide range of mechanical systems to facilitate the transfer of motion and force between two or more components. Its main purpose is to provide a high-friction surface that can be engaged or disengaged to control the motion of a system.
Friction lining is commonly used in automotive braking systems, industrial machinery, and other applications where controlled stopping or motion is required. When engaged, the friction lining creates a high-friction surface that resists the motion of the system, thereby slowing or stopping it.
In automotive braking systems, for example, the friction lining is applied to the brake pads, which are then pressed against the brake rotor to slow or stop the vehicle. The friction lining is designed to withstand high temperatures and wear, and to provide consistent and reliable braking performance over a wide range of operating conditions.
In industrial machinery, friction lining is used in a variety of applications, including clutches, brakes, and torque limiters. These systems use friction lining to engage or disengage mechanical components, control speed and motion, and protect against overloading and damage.
The material used to make friction lining is also important, as different materials have different properties and performance characteristics. Some common materials used for friction lining include organic, ceramic, and metallic compounds, each with their own advantages and disadvantages.
Overall, the function of friction lining is critical to the performance and safety of mechanical systems. By providing a reliable and consistent way to control motion and force, friction lining plays a vital role in ensuring that these systems operate effectively and efficiently.